Why Retailers Should Embrace New Supply Chain Technologies
By Tony Sinton, Netstock
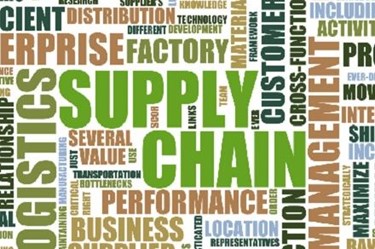
The 1st, 2nd and 3rd industrial revolutions were all built around some form of energy. The 1st fueled by steam, the 2nd by electricity and the 3rd by nuclear power. Enter the 4th Industrial Revolution, powered by smart, autonomous systems that use data and machine learning as their 'fuel.'
Requirements for different skillsets are becoming more and more prevalent. Job functions are starting to look a lot different as more companies begin to adopt new technologies such as robots, cobots, artificial intelligence, and Big Data. These technologies are making their way into the supply chain industry at an alarming rate and are creating previously unthinkable capabilities such as 24/7 connectivity, enhanced visibility, and efficiency.
The workplace of today faces significant disruption and begs the question – what should businesses be doing to embrace these changes? It's not so much that technology is the disruptor, it's when companies are not 'people-centric' – that is the biggest threat to any business. Companies need to take a peek into the future and envisage what their business would look like in an automated world. See what functions computers CAN'T do and how the workforce can integrate as opposed to being replaced by new technologies.
There is no doubt that specific jobs will be replaced as robotics, and automation can do many of the mundane work functions. Instead, look at roles that can be improved or augmented as opposed to being replaced. Consider, for example, the implementation of RFID tags on your inventory items. The job function of scanning the items will still exist, but the efficiency and visibility will be improved through the advanced line of sight and read rates available in RFID technology.
The business benefit is significant without any impact on the worker's job. Augmented Reality (AR) is another technology worth looking at. Think for a moment how you can improve your picker's efficiency by implementing augmented reality in the warehouse. AR will enable them to visualize exactly where a product is in the warehouse, saving time. AR used for staff training can dramatically reduce your training costs as staff can log in from anywhere in the world and learn how to operate heavy machinery or operate your robotic tools. No more expensive flights, accommodation, and training room costs. These are examples of how you can integrate technology in your workplace without losing your human capital.
Since data is the key driver in the 4th industrial revolution, data scientists and analysts will be in massive demand as will robotic and technology experts. Cybersecurity specialists are and will be in high demand. IoT devices and sensors come with incredible risk, so securing your supply chain from cyberterrorism will be a necessity. Current roles are also evolving - the Buyer of yesterday was skilled in transaction processing – the Buyer of tomorrow needs to understand commodity markets and have strong negotiation skills.
Freeing up staff's time spent on mundane tasks will allow them to focus on more essential tasks. Tasks like exploring new opportunities, improving high-level strategy, building relationships with customers, suppliers, and other stakeholders. Soft skills are unlikely to be replaced by technology as robots can't (yet) show empathy, nor do they possess a moral compass. Jobs related to building relationships are increasingly critical to a successful business and will always be in demand.
So, with all this in mind, encourage your employees to be flexible and to adapt their skillset to include soft skills like relationship building and problem-solving. Encourage them to embrace the changes coming their way and show them how they will fit into the broader business.
Ensure they understand that the 'future of work' is not a robot apocalypse but an era of human to machine collaboration. Companies need to look at how the future of their workforce and the future of their technologies align. Stay flexible in your approach and continue to evaluate priorities and tactics to evolve your future business and workforce structures effectively.
About The Author
Tony is the group CEO of NETSTOCK and cofounder of NETSTOCK, the first fully cloud-based inventory management solution. Tony provides strategy on supply chain management and has spent the last 27 years, enabling thousands of companies across the world to better manage their inventories.