Exploring The State Of The Retailer's Warehouse
By Valentyn Kropov, VP of Client Success, SoftServe
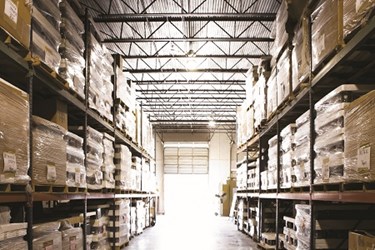
Discovering methods for warehouse and supply chain optimization is vital for the future of retail.
As technology advances, retailers are forced to evaluate their current business methods and systems, specifically the sophistication of the warehouse. A critical component of the supply chain, the overall goal of the warehouse is to achieve maximum efficiency and optimize productivity to meet the needs of the omni-channel retailer. As consumers become accustomed to full-cycle product offerings, they will be loyal to the retailer that offers what they want, when they want it. The warehouse must be refined to meet the supply chain challenges.
Assessing the current state, uncovering potential challenges, and then building upon strengths within the warehouse itself are vital for organic expansion and growth. Managers need to have the right tools to provide accurate data, insight, and trends to accurately diagnose and resolve issues.
Implementing a warehouse management system (WMS) is only the first step. Lost inventory, disparate systems, and inaccurate stocking predictions lead to the downfall of otherwise successful supply chains and warehouses, even when some technology is utilized. From here, retailers must improve upon the system’s inefficiencies in order to optimize the warehouse. In doing so, leaders will be able to accurately uncover the current state of the warehouse, identifying areas for improvement and optimization to make the right investments.
Lost Warehouse Inventory — Whose Fault Is It Anyway?
According to the 2016 National Security Survey, businesses in the United States lost $45.2B through inventory shrinkage in 2015. Inventory counts are most often performed annually, except in extreme cases such as fire or flood, or to satisfy an insurance claim. An annual count assumes that there is a problem of shrinkage without actual cause, only creating a greater productivity deficit amongst retail staff productivity. When implemented, advanced tools and technology at hand will help drive supply chain losses into a downward trend. Inventory loss — and its business impact — is steadily increasing for myriad reasons that extend beyond the warehouse.
- Employee theft is the sad reality when colleagues feel underpaid, underappreciated, or undervalued, and believe they are entitled to additional compensation via re-appropriating merchandise. Employees who engage in this type of behavior may be very adept at covering their tracks or passing losses off as clerical mistakes. When machine learning (ML) and artificial intelligence (AI) are integrated into the retailer’s current warehouse management system, ‘cheating the system’ will be infinitely harder, greatly reducing the warehouse’s amount of loss. For example, smart scales and cameras, using advanced AI/ML algorithms, will correctly count assets, making inventory shrinkage easily detectable. To learn more, read making the most of inventory counts.
- Administrative errors are less common as warehouses move to digital systems. But errors still occur and with significant cost implications. Proper training is required to ensure employees are familiar with the technology. Systems, processes, and workflow should be viewed holistically to mitigate such errors. Embedding siloed applications, with little or no interoperability, will create additional miscalculations and increase losses.
- External factors such as third-party suppliers like shipping and courier services, create another layer of impediment for retailers. Misplaced products, either intentionally taken or lost/damaged during transit, may result in unaccounted losses that go unseen for long periods of time, even if all deliveries are counted and recorded before entering the warehouse. AI/ML can be implemented in scale or camera image applications, providing an immediate record of incoming items and automatically report discrepancies.
Out Of Many Disparate Systems, Warehouses Need One
As technology poses new challenges, it also provides newer paths for resolution. Tomorrow’s retailers will soon discover the need for a truly single source of truth to fully understand how to overcome past hurdles and expand toward future growth.
Perhaps the largest hurdle for managers to overcome is simply trying to report on the data which is currently available. Most warehouses have several disparate inventory systems, ranging from manual/paper-based to more advanced software with analytics included. Reporting from one system only provides management with a glimpse into the current state of the warehouse and will not show the full picture.
To get started, warehouse management and IT staff should consider the following questions:
- What systems are currently in place? Which systems would benefit from technological improvements, such as AI/ML implementation?
- How is the data stored and protected? Can advanced security solutions, such as blockchain, be beneficial to the process?
- How can reporting from the different areas be combined to provide a full view of warehouse operations?
Always Looking Ahead
The next step in warehouse optimization looks to the future to make accurate demand predictions — ensuring the right quantities are available at the right times.
For example, a tire dealership must keep certain tires in stock, especially around peak travel seasons. When shopping for tires, most drivers will replace all four tires at once. This information tells the warehouse to keep tires stocked in quantities of four. However, there will be purchases of single tires, breaking up sets of four. The system needs to be capable of making these associations and reorder in real time to ensure the optimum quantities are always in stock.
Likewise, a big box retailer may be preparing for warmer months by stocking outdoor items, such as gas grills. While seasonal stocking may be standard for many WMS systems, advanced applications should be able to proactively inform management of related items, most frequently purchased together. For instance, from the obvious grill covers or propane tanks to more obscure trends, such as patio lawn furniture.
In Conclusion
Over the next decade, warehouses must build on effective process-driven technologies to optimize the software currently in place and plan for upgrades. Uncovering the state of the warehouse starts with a detailed analysis of current processes, before revealing opportunities for future growth and technological advancements.
- First leaders need to identify key areas where warehouse stock may be lost, such as theft, clerical errors, or third-party inaccuracies. Installing AI/ML tactics into the current WMS will replace human issues and errors, whether caused by accident or with intent.
- Integrating the current disparate systems, with a focus on data management and security, will only become a reality once data warehouses and analytics are available to guide the supply chain and warehouse. Using innovative technology, such as blockchain, will ensure that the company’s valuable information is not exposed, leading to severe negative consequences.
- The final step to address is incorporating a demand prediction tool. This allows retailers to address the future needs of their consumers and ensure the warehouse is appropriately stocked.