How 2018 Tax Changes Will Impact Supply Chain's Bottom Line
By Brian Holland, Fleet Advantage
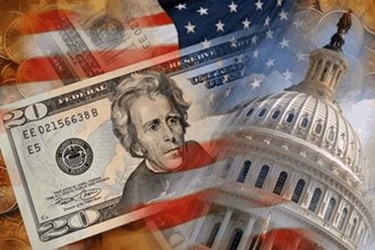
America’s corporations with transportation fleets and supply chain operations continue ordering units at an increased pace. The latest figures from ACT Research show orders for Class-8 trucks surged to an all-time high in July for North American Fleets (52,000 trucks). In the first seven months of the year, 300,000 Class 8 truck orders were placed by such fleets — the largest figure since 2004.
It’s critical for organizations to replace their aging equipment for multiple reasons, especially since the American economy continues to rely heavily on truck deliveries and commercial drivers. According to the Bureau of Transportation Statistics, more than $1 of every $10 produced in the U.S. GDP can be directly tied back to transport activity. Also, The American Trucking Association indicates trucks contain 70 percent of America’s freight (by weight).
That said, organizations must be cognizant of 2018 tax changes because the way they procure their equipment can have a significant impact to their overall business, bottom line and financial performance.
What Are The Impending Tax Changes?
The tax plan proposed by the current administration contains several provisions that will impact equipment acquisition — lower tax rates for businesses, non-deductibility of interest expense for C corporations, limiting like-kind exchanges to real property, and expensing of depreciable assets instead of writing them off over years. While it’s hard to say how much of this ultimately gets implemented, the key is to know how these changes may impact a company’s balance sheet, financial plan, and tax strategy, and to adjust accordingly to help improve the company’s financial performance.
In terms of what is being proposed, the corporate tax rate would be cut to 21 percent, and a proposal to allow for immediate write-off for equipment. As an example, bonus depreciation is doubled to 100 percent and companies can write-off the full amount of qualifying purchases in the same year of acquisition, which is intended to spur investment. In addition, used equipment will qualify for bonus depreciation for the first time. Companies can continue to deduct the cost of leased assets and the tax benefits inherent in tax-advantaged leases get passed along to the lessee through lower pricing. Lessees also will enjoy lower tax rates that will help them expand their business.
In many cases, a lease is still favorable over a loan for acquiring equipment. Under the new U.S. accounting rules, customers with Operating Leases will find that the capitalized asset cost is lower compared to a loan or cash purchase. Why? Because the balance sheet presentation of an Operating Lease reflects only the present value of the rents due under the contract as the asset amount, and as a result, it is still “partially” off-balance sheet.
In addition, since the cost of an Operating Lease is reported as a straight-line expense of the full lease payment each period, there is no front-end loaded P&L impact that comes from expensing depreciation and imputed interest costs as there is when a customer borrows to make an outright asset purchase. The P&L impact is different under the international accounting standards (the expenses are front-end loaded), but the result under both standards is that leasing — compared to borrowing to buy — will show a better Return on Assets (ROA), Return on Invested Capital (ROIC), or Return on Capital Employed (ROCE) for the lessee, which are measures used by many companies and equity analysts.
Moreover, consider the discounted cost and built-in flexibility of financing, which offer additional savings, extended payment options and equipment upgrades or add-ons. Improved cash-flow management, keeping pace with technology and aligning capital asset acquisition strategy with business needs in real time all create economic and practical advantages compared to a loan.
Procurement Strategies Remain Critically Important
Private fleet organizations and for-hire carriers must still pay close attention to the way in which they procure new trucks, especially under the changing tax environment. Many organizations have begun to lease more of their trucks, whereby a shorter asset management life cycle helps reduce costs significantly. Everything from lower fuel costs, maintenance and repair, and disposal costs are reduced in a leasing environment, while the residual risk is minimized.
Companies are taking an even closer look now at how procurement and how certain equipment lease structures impact their overall financial performance. Knowing the intricacies of different types of leases (operating vs. capital, for example) can help achieve better key performance financial metrics significantly.
The Bottom Line
Whether through economic expansion forthcoming by the proposed tax cuts or a desire to replace aging trucks, more businesses today are focused on truck procurement strategies. Decisions such as lease versus purchase, the type of lease, as well as changing tax implications can all have consequential effects to an organization’s bottom line.
About The Author
Brian Holland is President and Chief Financial Officer at Fleet Advantage, a leading innovator in truck fleet business analytics, equipment financing and life cycle cost management. For more information visit www.FleetAdvantage.com.