Traceability: The Solution To Product Recalls
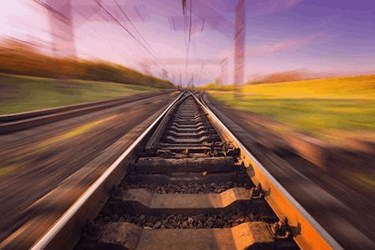
By Gary Barraco, Director, Global Product Marketing, Amber Road
According to the U.S. Consumer Product Safety Commission (CPSC), recalls that should put consumers on high alert occur daily. Consumers beware:
- Drawstrings that cause choking.
- Ingesting baby rattle contents.
- Fire-sparking cellphone batteries.
- Electric-shocking power adapters.
It seems product recalls are now the norm on a wide range of products from cellphones to ATVs, high heels, children’s clothing, and more. In one week, the CPSC reported several recalls on its website: incorrect venting Nutrilife® hydrogen peroxide bottles cause fires or burns; melting hoses in Academy Sports + Outdoors pet crawfish kits; cracking rings on BRIO baby rattles cause choking; and tires blowing out on Polaris’ recreational off-highway vehicles cause crashes.
Recalls are a nuisance for consumers but have serious repercussions for a brand or manufacturer. They can cause brand blemish, unexpected operational burdens, and costly remediation. I recently met with a senior executive from Samsung and we discussed the impact on the organization’s transportation side from the Galaxy Note7 recall. He urged me to think about the return shipping process for over 2.5 million units. The published estimated cost for the entire product recall: $17 billion.
The complexity of today’s global supply chains only means an increasing vulnerability to unexpected supply disruptions, with more suppliers and contract manufacturers added into the supply chain. Yet many companies fail to leverage technology and integration to properly manage events like recalls, CPSC or Customs product holds, or consumer/NGO inquiries.
The Solution? Traceability
Better product traceability can help better manage recalls. Here is how we define traceability: having the capability to connect the dots between the raw materials supplier, finished good manufacturer, product, and purchase order. This level of detail, provided in a digital supply chain environment, can also help to manage social and environmental responsibilities, enhance product quality, and maintain regulatory compliance.
Traceability is typically comprised of two elements to produce reliable, high-quality products that loyal consumers expect:
- It’s an imperative for manufacturers, retailers, importers, and distributors to proactively evaluate and test textiles, trim, and components in the products they sell to ensure they are producing goods using materials that meet regulations.
- Companies also need to document all of the activities related to product compliance based on global regulations and at times provide consumer-accessible systems to trace raw material components in goods and or production facility information.
Pre-Emptive Strike Back
When products are recalled, brands need to have the ability to trace every order back to the supplier — and even the supplier’s supplier in most cases. This means tracing back to where the product was manufactured, what materials went into the finished good, and where these materials are used in current or completed orders. This level of visibility and control helps brands and retails react to problems when they spring up with the data necessary to avoid supply chain failure.
Technology gives companies the edge and advantage to take preventative measures through visibility and reporting. With a pre-emptive process, brands can anticipate and respond promptly to issues by managing controlled risks. They can focus on uncertainties rather than certainties, and point to problems that need attention when a reactive measure is necessary.
By using digitized data about the raw material components that go into each product, in conjunction with a collaborative solution during product design and technical design, brands can reduce the risk of recalls, the need for product redesigns or other costs that can be avoided.
Staying In Compliance
Collaboration with external suppliers is required to maintain ethical and regulatory standards. During the production, packaging and shipment processes, finished goods can deviate from “in compliance” components to a “non-compliant” item. Examples might include packaging of a children’s item that is not within government standards to avoid suffocation risk or the addition of embellishments that were not considered during the design process but contain unsafe material composition.
Technology can enable product and component inspections to be scheduled with third-party inspection companies, or in-factory spot checks can employ XRF scanners to ensure the raw materials being used are not out of compliance. Online inspection forms are then attached to these requests, providing the inspector with the detailed inspection requirements. When complete, these forms can be printed and/or shared electronically for the tracking of production quality and compliance results.
This level of collaboration enforces consistent standards and gives the brand the ability to lock down activity with non-compliant suppliers. Key Performance Indicator scorecards based on supplier performance and product quality provide an effective solution to spot any trends that need to be addressed. These are pre-emptive measures that allow for corrective action in the future.
Better Visuals
With reporting and mapping tools, supply chain managers can visualize their primary supply and feeder streams. Based on the data unified from product, factory and raw material orders in this platform, traceability enters the picture. Compliance managers can identify areas where compliance risk is most prevalent based on historical data — where has the supply chain failed — and alter the course to alleviate future failures.
More importantly, when a recall or safety issues pops up, managers can trace it to the origination point. Action can then be taken to attempt to minimize the current breakdown and verify which products have been affected. To reach this level of “all-encompassing” product safety and compliance, integration between the technology solutions in use is crucial.
As a packaged solution that unifies PDM, PLM, and global trade management tasks, companies need a means for users — including internal sourcing, quality assurance and legal teams, overseas buying offices, suppliers, agents, external inspectors, and others — to achieve greater visibility into the processes.
These solutions can help companies in their efforts to re-evaluate business strategies, gain a better understanding of the critical interdependencies and supply chain risks along the way — from the sourcing of raw materials to delivery to the customer — and act to prevent these risks before they happen, or appropriately manage the response when they do.